Plastic extrusion for high-strength, durable materials
Plastic extrusion for high-strength, durable materials
Blog Article
A Comprehensive Overview to the Process and Benefits of Plastic Extrusion
In the vast realm of manufacturing, plastic extrusion emerges as a highly effective and crucial process. Transmuting raw plastic into continual accounts, it caters to a variety of markets with its amazing convenience.
Recognizing the Essentials of Plastic Extrusion
While it might show up complex initially glance, the procedure of plastic extrusion is basically straightforward - plastic extrusion. It is a high-volume production strategy in which raw plastic is thawed and shaped right into a continuous account. The process begins with the feeding of plastic product, in the type of pellets, granules, or powders, right into a warmed barrel. The plastic is after that melted making use of a mix of warmth and shear, used by a turning screw. Once the molten plastic gets to the end of the barrel, it is required with a tiny opening called a die, shaping it right into a wanted form. The designed plastic is after that cooled, strengthened, and cut into wanted lengths, finishing the process.
The Technical Refine of Plastic Extrusion Explained
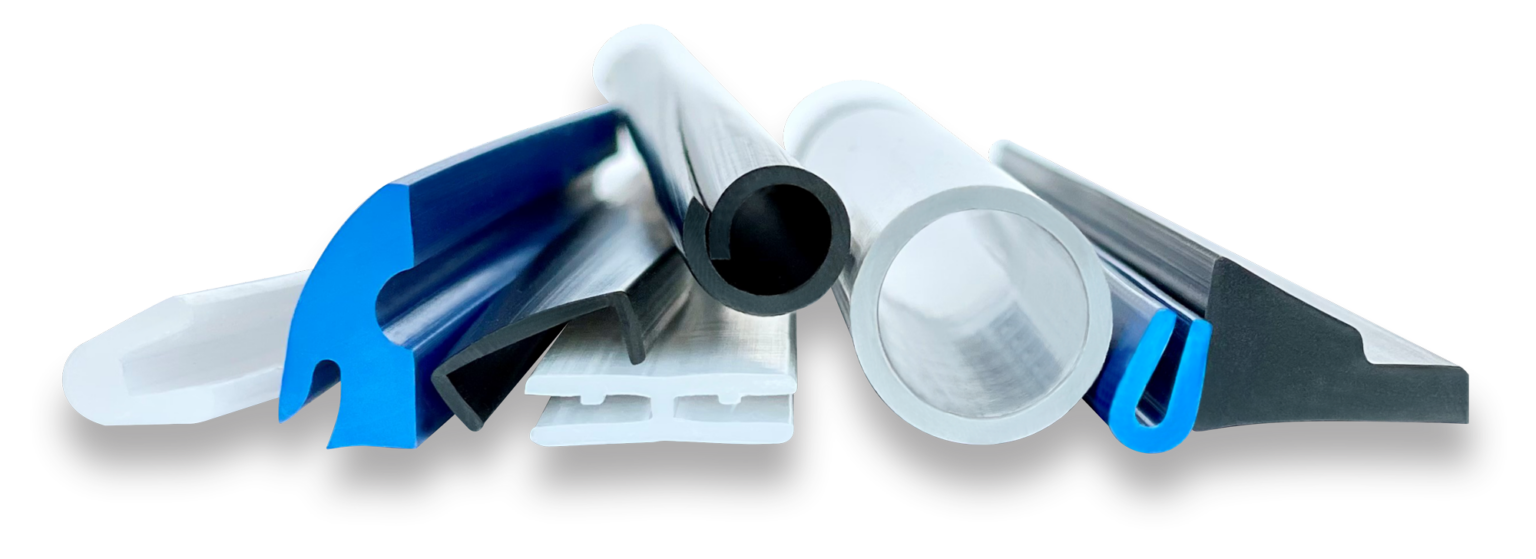
Kinds Of Plastic Suitable for Extrusion
The option of the right sort of plastic is a crucial element of the extrusion procedure. Various plastics offer one-of-a-kind residential properties, making them much more suited to specific applications. Polyethylene, as an example, is typically utilized due to its affordable and simple formability. It provides excellent resistance to chemicals and moisture, making it optimal for items like tubing and containers. In a similar way, polypropylene is an additional preferred option due to its high melting factor and resistance to fatigue. For even more durable applications, polystyrene and PVC (polyvinyl chloride) are usually picked for their stamina and longevity. These are usual alternatives, the choice eventually depends on the specific needs of the product being produced. Comprehending these plastic kinds can significantly boost the extrusion procedure.
Contrasting Plastic Extrusion to Various Other Plastic Forming Methods
Understanding the sorts of plastic ideal for extrusion leads the way for a wider discussion on how plastic extrusion piles up against various other plastic developing approaches. These include shot molding, strike molding, and thermoforming. Each approach has its distinct usages and advantages. Injection molding, for circumstances, is outstanding for developing complex parts, while blow molding is excellent for hollow things like bottles. Thermoforming excels at creating huge or superficial parts. However, plastic extrusion is unparalleled when it comes to producing continuous accounts, such as pipes, gaskets, and seals. It also enables a constant cross-section along the length of the product. Therefore, the option of approach greatly depends upon the end-product demands and specifications.
Trick Advantages of Plastic Extrusion in Manufacturing
In the realm of production, plastic extrusion supplies many substantial benefits. One remarkable benefit is the cost-effectiveness of the process, which makes it an economically enticing production method. Furthermore, this technique provides superior product versatility and enhanced production speed, consequently raising general manufacturing effectiveness.
Economical Manufacturing Technique
Plastic extrusion leaps to the forefront as a cost-effective production approach in production. This process stands out for its capacity to generate high volumes of product promptly and successfully, providing makers with substantial financial savings. The primary cost benefit is the capability to utilize less costly basic materials. Extrusion uses polycarbonate products, which are much less expensive compared to metals or porcelains. Further, the extrusion process itself is reasonably basic, decreasing labor costs. Furthermore, plastic extrusion needs much less power than traditional manufacturing approaches, adding to lower functional costs. The procedure also reduces waste, as any additional resources faulty or excess materials can be reused and reused, offering one more layer of cost-effectiveness. Generally, the economic benefits make plastic extrusion a very appealing alternative in the manufacturing sector.

Superior Item Flexibility
Beyond the cost-effectiveness of plastic extrusion, one more significant advantage in producing depend on its remarkable item adaptability. This process permits for the creation of a large variety of items with differing shapes, styles, and sizes, from easy plastic sheets to elaborate accounts. The versatility is credited to the extrusion die, which can be tailored to yield the preferred item style. This makes plastic extrusion an ideal solution for markets that require tailored plastic parts, such as auto, construction, and packaging. The ability to create varied items is not just advantageous in meeting particular market needs however also in allowing producers to discover brand-new line of product with very little resources financial investment. In essence, plastic extrusion's product versatility fosters development while boosting functional efficiency.
Enhanced Manufacturing Speed
A considerable benefit of plastic extrusion hinges on its boosted manufacturing rate. This production procedure permits for high-volume production in a fairly short time span. It is capable of producing long, continuous plastic accounts, which significantly lowers the production time. This high-speed production is especially beneficial in sectors where huge amounts of plastic components are needed within limited due dates. Few various other production processes can match the rate of plastic extrusion. Additionally, the capacity to maintain consistent high-speed manufacturing without sacrificing product quality sets plastic extrusion apart from various other techniques. The boosted production rate, therefore, not only makes it possible for makers to meet high-demand orders but likewise adds to enhanced efficiency and cost-effectiveness. This beneficial attribute of plastic extrusion has actually made it a recommended selection in countless industries.
Real-world Applications and Effects of Plastic Extrusion
In the realm of manufacturing, the strategy of plastic extrusion holds profound relevance. The economic advantage of plastic extrusion, mostly its high-volume and affordable output, has revolutionized manufacturing. The sector is constantly aiming for technologies in eco-friendly and recyclable materials, showing a future where the advantages of plastic extrusion can be preserved without compromising environmental sustainability.
Conclusion
Finally, plastic extrusion is a reliable and very efficient approach of transforming basic materials into varied products. It uses various advantages over other plastic a fantastic read developing methods, consisting of cost-effectiveness, high outcome, minimal waste, and layout versatility. Its effect is profoundly really felt in numerous sectors such as building and construction, auto, and customer items, making it an essential procedure in today's manufacturing landscape.
Diving deeper into the technical process of plastic extrusion, it begins with the selection of the suitable plastic product. Once cooled, the plastic is cut into the needed sizes or wound onto reels if the item is a plastic film or sheet - plastic extrusion. Contrasting Plastic Extrusion to Other my review here Plastic Forming Techniques
Comprehending the kinds of plastic suitable for extrusion leads the means for a wider discussion on how plastic extrusion stacks up versus other plastic creating methods. Few other production procedures can match the rate of plastic extrusion.
Report this page